Recubrimiento PVD
INVEST PLASMA consigue efectos metalizados sobre diferentes volúmenes y materiales como por ejemplo la cerámica, el metal, el plástico, etc, gracias a la tecnología PVD para aplicaciones decorativas, técnicas e industriales.
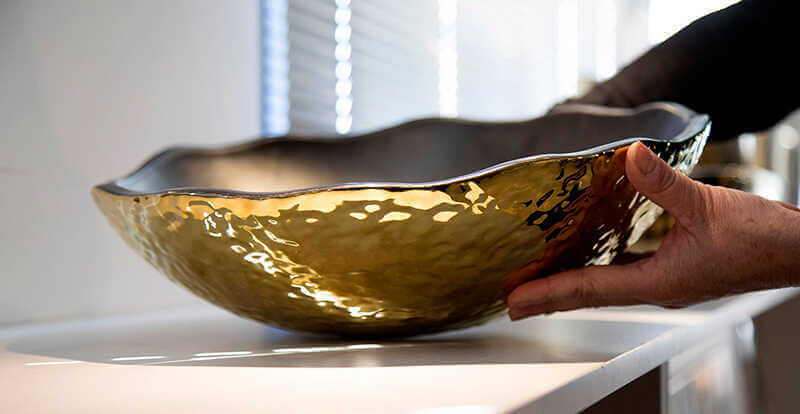
ÍNDICE
¿Qué es PVD?
La deposición en fase de vapor por método físico, conocida como PVD por sus siglas en inglés – Physical Vapour Deposition -, es una tecnología respetuosa con el medio ambiente que engloba cualquier proceso de crecimiento de una película de recubrimiento en un ambiente de vacío, que implique la deposición de átomos o moléculas sobre un sustrato.
Dentro de una cámara de vacío, se vaporizan diferentes metales como titanio, circonio y cromo, entre otros, y se condensan en la superficie del producto dándole el recubrimiento perseguido, ya sea decorativo con una amplia gama de colores como técnico facilitando una alta dureza, resistencia a la abrasión, ralladuras y corrosión.
Revestimiento PVD
El revestimiento en vacío está sustituyendo los métodos de revestimiento tradicionales en muchas áreas de aplicación, como la galvánica. La flexibilidad de esta técnica permite revestir todo tipo de material independientemente de la forma, geometría y dimensiones.
A través de este proceso se obtienen objetos técnicos y decorativos mucho más brillantes, perfectamente reflectantes, de aspecto metálico y pueden pintarse de varios colores. Además de la elevada resistencia de las superficies, se obtiene un aspecto decorativo duradero en el tiempo.
Tecnología PVD
De las distintas técnicas de PVD que existen en el ámbito de los tratamientos superficiales, a nivel decorativo cabe destacar las denominadas PVD por arco catódico, pulverización magnetofónica y fuente de plasma.
Evaporación por arco catódico (CAE)
El proceso PVD por arco catódico consiste en la evaporación de un metal puro o aleación en la obtención de su reacción con gases industriales para la formación del compuesto deseado (color), y en la deposición sobre la pieza a recubrir (sustrato).
Previamente, en la cámara del reactor se obtiene un grado de vacío del orden de 10-5 mbar. La deposición puede producirse en una atmósfera reactiva o inerte, y es preferible que el sustrato se mantenga a temperatura (fase de precalentamiento) para incrementar los valores de adherencia.
Los átomos o moléculas de un material son vaporizados desde una fuente sólida, transportados en la forma de vapor en una atmósfera gaseosa a baja presión y por último, son condensados sobre una superficie para formar el recubrimiento.
Nuestros recubrimientos metálicos son producidos utilizando el proceso de evaporación por arco catódico, en el cual generamos un arco eléctrico con alta corriente y bajo voltaje para erosionar un electrodo catódico sólido. El arco se mueve sobre el cátodo generando calentamiento local y vaporización de átomos. Tales átomos pasan a través de una nube electrónica donde se ionizan. Las partes a recubrir se polarizan negativamente, de esta forma atraen a los iones generados, lo que resulta en la formación del recubrimiento en la superficie
Pulverización magnetrónica (MS)
En la MS, iones de argón acelerados impactan sobre un metal sólido (objetivo) y provocan la expulsión (evaporación) de material por acción mecánica. También en este caso el metal evaporado puede recombinarse con el gas de proceso, en forma de plasma, para crear un depósito de película delgada sobre los productos que giran dentro de la cámara de vacío (pulverización reactiva). Existen diferentes configuraciones de Pulverización magnetrónica posibles, según la fuente de energía y la configuración del campo magnético:
- Pulverización con magnetrones equilibrados
- Pulverización magnetrónica dual (DMS)
- Pulverización magnetrónica pulsada dual
- Pulverización con magnetrones no equilibrados (UBM)
- Pulverización magnetrónica RF
- HIPIMS, etc.
La geometría del objetivo puede ser plana, circular o, en algunos casos, también cilíndrica.
Fuente de plasma (PBS)
La fuente de plasma se utiliza principalmente en recubrimientos por PECVD. Gracias a esta tecnología, el plasma es más denso y más energético para obtener recubrimientos de mayor calidad.
Ventajas de la fuente de plasma: Mayor calidad y uniformidad, Temperatura más baja, Uso innovador de gas o vapor (precursores), Recubrimiento menos tensado y el mayor espesor posible, Mayor velocidad de recubrimiento comparado con la PECVD estándar
Máquina de arco catódico
Máquina magnetrón
Invest Plasma: Liderazgo en recubrimientos PVD en España
En Invest Plasma somos líderes en tecnología PVD en España, ofreciendo soluciones avanzadas y personalizadas en recubrimientos para aplicaciones técnicas, decorativas e industriales.
Con años de experiencia en el sector, implementamos procesos de recubrimiento basados en tecnología de vanguardia, diseñados para garantizar alta resistencia, durabilidad y acabados estéticamente impecables. Apostamos por un modelo de sostenibilidad que combina innovación tecnológica con el uso de materiales respetuosos con el medio ambiente, asegurando resultados de máxima calidad en cada proyecto.
Si buscas una empresa confiable y experta en PVD en España, en Invest Plasma estamos comprometidos con ofrecer soluciones que superen las expectativas del mercado y aporten valor real a tus productos.
Proyectos PVD: Innovación personalizada
Nos especializamos en la ejecución de proyectos PVD diseñados para satisfacer las necesidades específicas de nuestros clientes. Hemos llevado a cabo proyectos que abarcan recubrimientos en metales, cerámicas y plásticos, logrando acabados resistentes al desgaste, a la corrosión y con una amplia gama de opciones estéticas, incluyendo superficies brillantes, mate y coloraciones personalizadas.
Cada proyecto es gestionado con un enfoque integral, desde la selección de materiales hasta la implementación de procesos que garanticen resultados consistentes y de alta calidad.
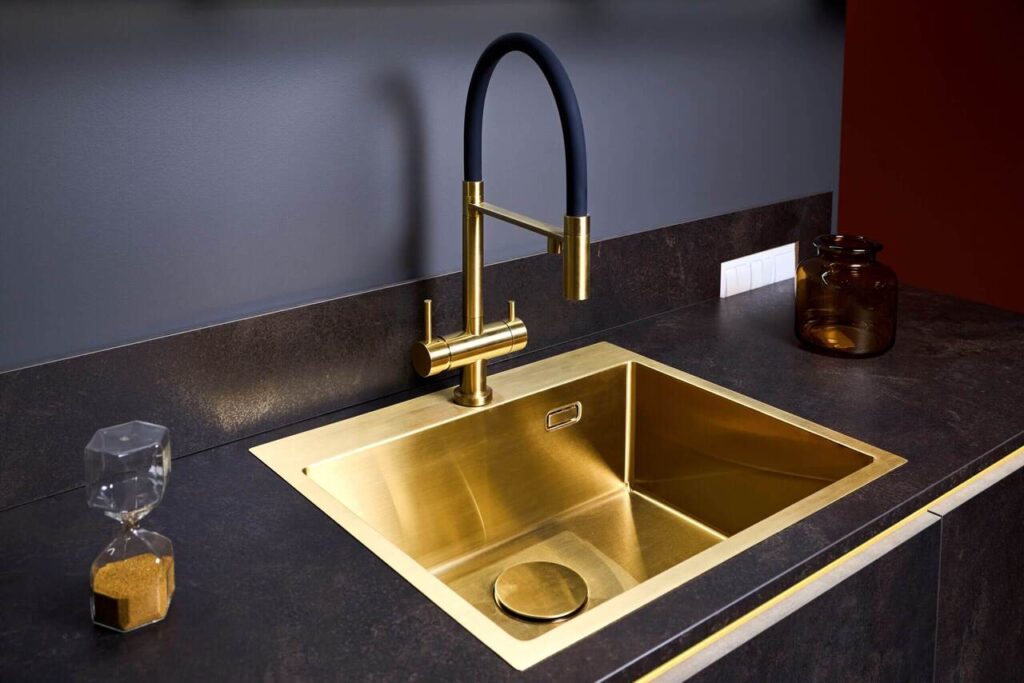
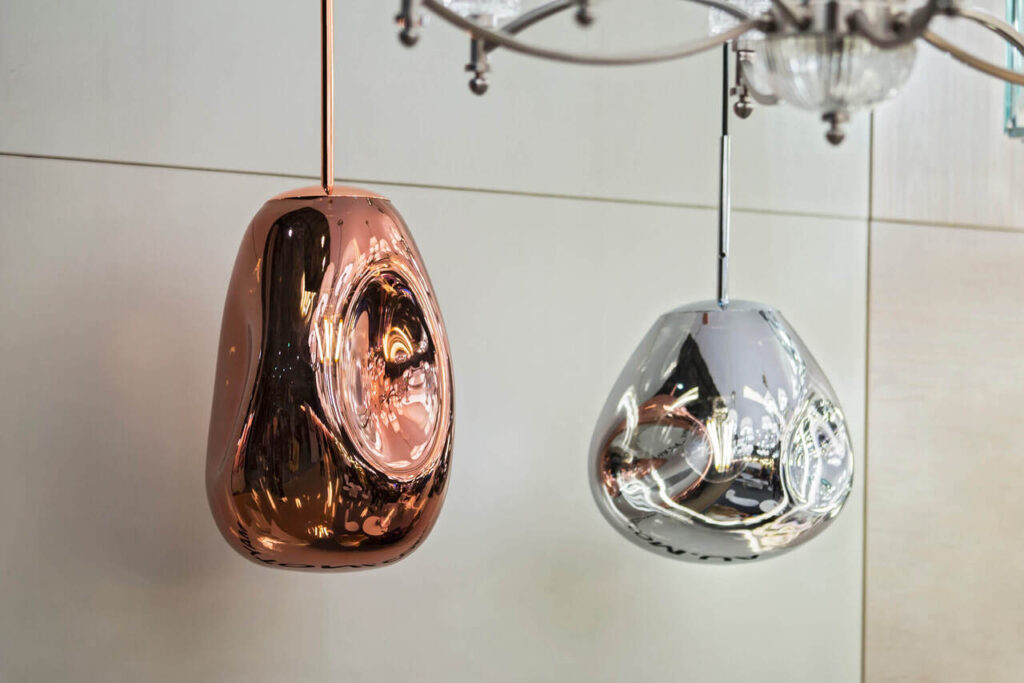
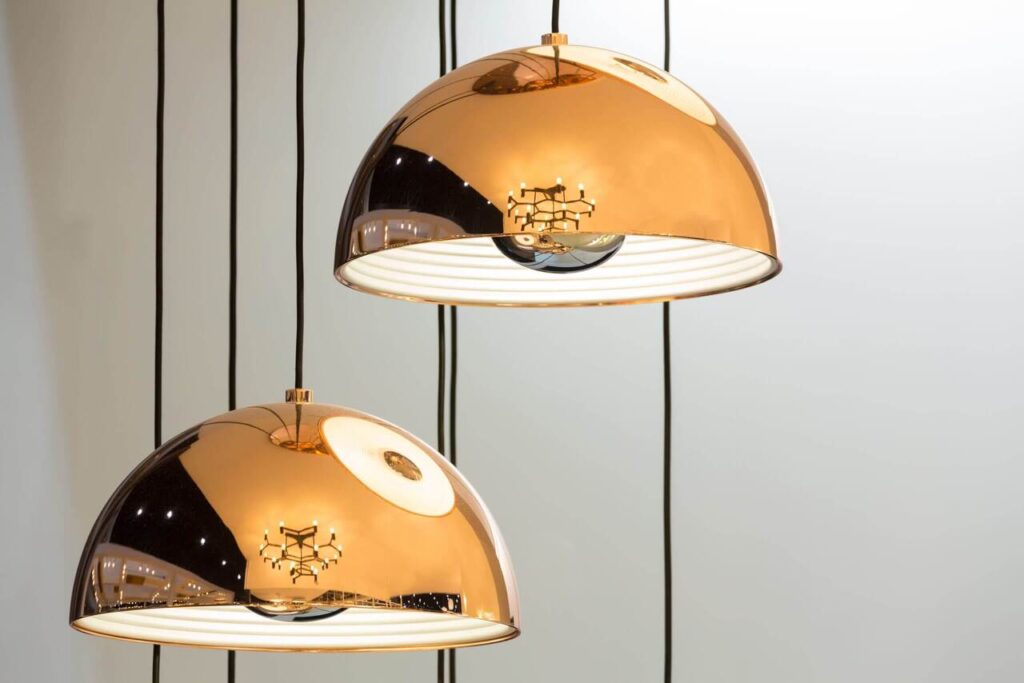
FAQ habituales acerca del PVD
-
¿Cuáles son los beneficios del acabado PVD?
El acabado PVD proporciona alta dureza, resistencia al desgaste y un atractivo visual mejorado. Es ideal para aplicaciones técnicas y decorativas.
-
¿Qué materiales se pueden recubrir con PVD?
Materiales como metal, cerámica y plástico son compatibles con el recubrimiento PVD, ofreciendo resultados de alta calidad y personalización.
-
¿Qué es el PVD decorativo?
El PVD decorativo se utiliza para lograr acabados coloridos y brillantes, ideales para productos de lujo y diseño innovador.
-
¿Cuál es el uso del titanio PVD?
El titanio PVD es ampliamente utilizado en aplicaciones técnicas debido a su alta resistencia a la corrosión y su atractivo acabado metálico.
-
¿Cuál es el precio de un proyecto PVD?
El precio de un proyecto PVD varía dependiendo de factores como el tipo de material a recubrir, el tamaño del producto, el tipo de recubrimiento requerido (decorativo o técnico) y el volumen del pedido. En Invest Plasma ofrecemos presupuestos personalizados para cada cliente, asegurándonos de que el costo refleje la calidad y la precisión de nuestro trabajo. Para obtener un presupuesto específico, te invitamos a contactarnos y compartir los detalles de tu proyecto.